Injection Moulding Manufacturer: Quality Solutions for Your Business Needs
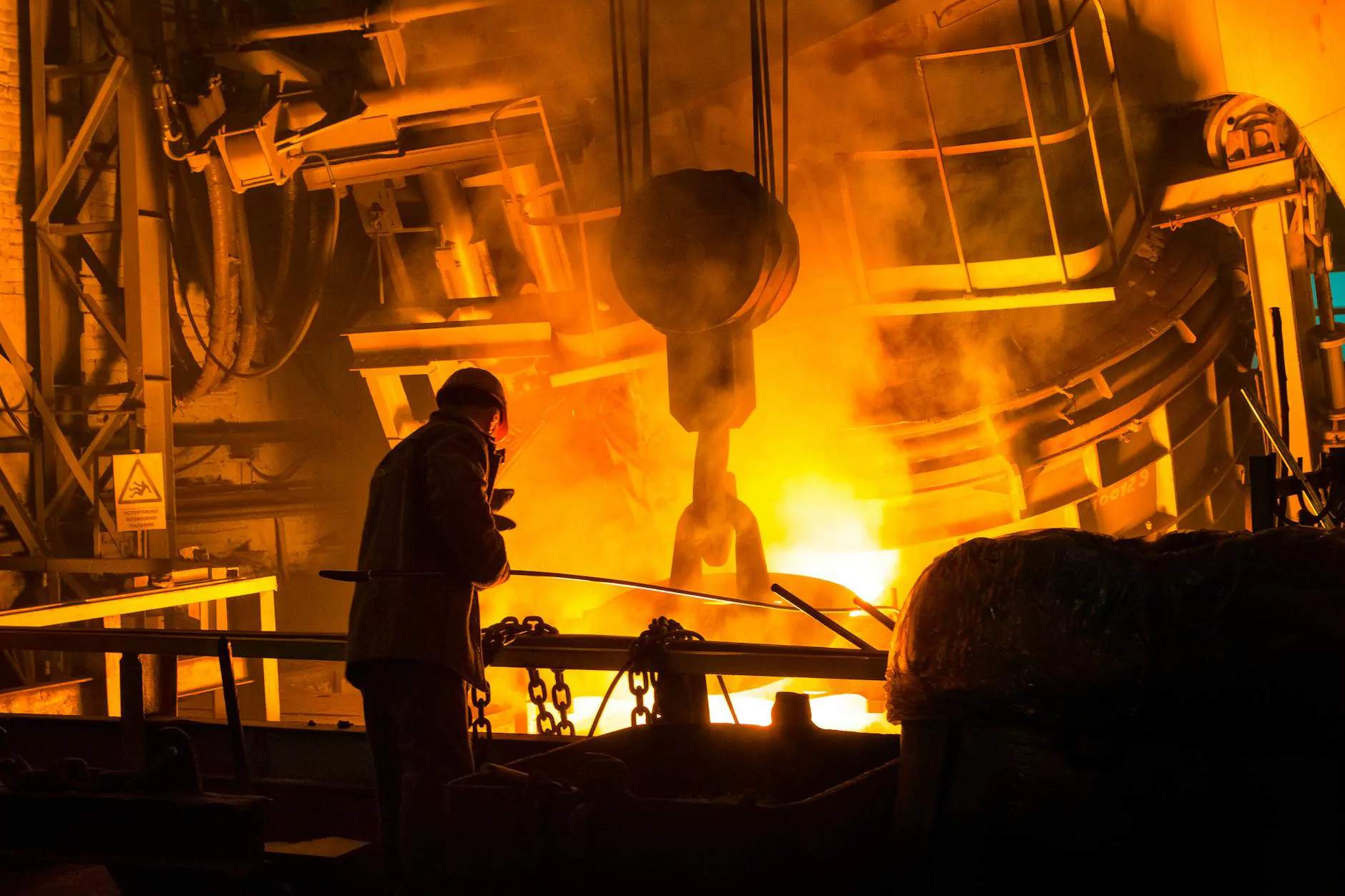
The world of manufacturing is rapidly evolving, and injection moulding manufacturers are at the forefront of this transformation. As a vital component in the production of various plastic parts, injection moulding offers incredible advantages that have made it a preferred choice for industries ranging from automotive to consumer goods. In this article, we will explore the significance of injection moulding, the benefits of working with an experienced manufacturer, and the intricacies of the injection moulding process.
Understanding Injection Moulding
Injection moulding is a manufacturing process used for producing parts by injecting molten material into a mould. It is a highly efficient method that allows high-volume production with exceptional precision. Here’s how it works:
- Material Preparation: The process begins with the selection of the appropriate plastic material, which can be in the form of pellets or granules.
- Heating: The plastic is heated in an injection unit until it reaches a molten state.
- Injection: The molten plastic is then injected into a pre-designed mould.
- Cooling: Once injected, the plastic cools and solidifies to take the shape of the mould.
- Ejection: After cooling, the mould is opened, and the newly formed part is ejected.
The Benefits of Using an Injection Moulding Manufacturer
Engaging with a reputable injection moulding manufacturer offers numerous benefits that can significantly impact your business operations. Here are some key advantages:
- Cost-Effectiveness: High-volume production reduces per-unit cost, making it an economical choice for mass manufacturing.
- Precision and Accuracy: Advanced machinery and technology ensure consistent results and high-quality parts with tight tolerances.
- Material Versatility: Manufacturers have access to a wide range of plastic materials, allowing flexibility in design and application.
- Rapid Production: Injection moulding is known for its speed, enabling manufacturers to meet tight deadlines.
- Scalability: The process can easily be scaled up or down to accommodate different production needs.
Key Applications of Injection Moulding
The versatility of injection moulding makes it applicable across various industries. Here are some notable applications:
1. Automotive Industry
In the automotive sector, injection moulding is used to create numerous components such as dashboard panels, interior trim, and even specialized parts for electric vehicles. The lightweight nature of plastic parts contributes to improved fuel efficiency and performance.
2. Consumer Electronics
From smartphone cases to intricate electronic housings, injection moulding facilitates the production of aesthetically pleasing and functional designs that adhere to strict industry standards.
3. Medical Devices
Safety and precision are paramount in healthcare. Injection moulding enables the production of critical medical devices and components with high accuracy and reliability, catering to the stringent regulations of the medical industry.
4. Household Products
Everyday items such as containers, kitchen gadgets, and toys are often manufactured using injection moulding, highlighting its importance in our lives.
Choosing the Right Injection Moulding Manufacturer
Not all injection moulding manufacturers are created equal. Here are some essential factors to consider when selecting a partner for your manufacturing needs:
- Experience and Expertise: Look for a manufacturer with a proven track record and expertise in your specific industry.
- Technology and Equipment: Ensure the manufacturer utilizes modern and advanced machinery for optimal results.
- Quality Assurance: A reputable manufacturer should have rigorous quality control processes in place to maintain consistency.
- Customization Options: Every business has unique needs. Choose a manufacturer that offers tailored solutions and can accommodate your specific requirements.
- Customer Support: Responsive and knowledgeable customer service is crucial for addressing any concerns and ensuring a smooth manufacturing process.
The Future of Injection Moulding
As technology progresses, the field of injection moulding continues to evolve. Below are some advancements and trends shaping the future of this manufacturing process:
1. Automation and Smart Manufacturing
The integration of automation and Industry 4.0 principles is revolutionizing the injection moulding landscape. Automated systems can enhance production efficiency, minimize human error, and allow for real-time monitoring of the manufacturing process.
2. Sustainable Practices
With the growing emphasis on sustainability, manufacturers are increasingly adopting eco-friendly materials and practices. Biodegradable plastics and recycling initiatives are becoming more prevalent in the injection moulding industry.
3. Advances in Materials
Research and development in new materials are paving the way for stronger, lighter, and more durable plastic parts. Innovations such as composite materials and high-performance plastics are expanding the possibilities of injection moulding applications.
Conclusion
In conclusion, partnering with a proficient injection moulding manufacturer can unlock numerous benefits for your business. Whether you operate in the automotive sector, consumer electronics, or any other industry, the advantages of this manufacturing process are undeniable. With cost-effectiveness, precision, and rapid production capabilities, injection moulding stands out as a premier choice for businesses aiming to enhance their product offerings.
As you explore your options, consider the future trends and technologies that might influence your manufacturing decisions. Embrace the potential of injection moulding and take your business to new heights.
For more information about how an expert injection moulding manufacturer like Deep Mould can assist your business, visit deepmould.net and discover tailored solutions that meet your needs.